PRODUCT OVERVIEW
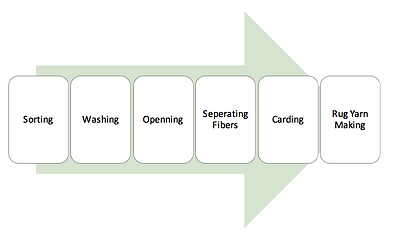
Figure 1: Information from Belfast Mini Mills
Belfast Mini Mills produces sixteen different machines, with add ons, that can aid in the production of various textiles by using small batches of fibre (Belfast Mini Mill). The basic mill that would be sent to Nepal would include a washer, picker, carder and a rug yarn maker to create rug yarn as a final product. Without using the rug yarn marker, the wool can be made into other textile creations (R., 2016). The process for creating rug yarn can be seen in figure 1.
A washer from Belfast as seen in figure 2, is a fibre washing system that potentially can wash 3 different fibre types or colours that can weigh up to 21 pounds in one system operation Belfast Mini Mill, 2009). Advantages to this washer system include customizable options such as water levels and cycle choices when processing different types of fibres to insure a higher quality and cleaner fibre stock (R., 2016). It includes 8 cycles as well as an option to customize the amount of soap used depending on the cleanliness of the fibre to help reduce the price of production (R., 2016) .
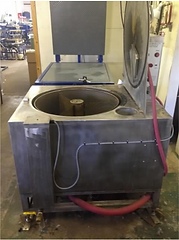
Figure 2: Washer from Belfast Mini Mill website
A picker (figure 3) is used on already washed fibre after drying has completed, this machine teases out tangles in the fibre to create a consistent stock, or a blended fibre stock (R., 2016). By opening the fibre with this machine it creates a piece of processed fibre which has a consistent colour and thickness. This machine creates a cloud of fibre, with no vegetation by vacuuming the fibres before output. After picking the fibres, conditioning oils are used to soften fibres before the next stage begins (R., 2016).
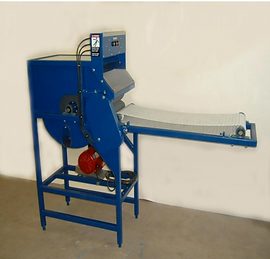
Figure 3: Picker from Belfast Mini Mill website
The carder is used to make felts and rug yarn, but another machine can be replaced or added to create fibres used for another type of textile creation as seen in figure 4 (Belfast Mini Mill, 2009). The carder separates fibres and aligns them as a continuous web for output, which is either used to create batts, which is primarily used for felt and rug making operations, or rovings which can be made into balls of wool. Since the carder creates a wool with a large diameter, another machine can be used to reduce the wool diameter and create a finer fibre (Belfast Mini Mill, 2009).

Figure 4: Carder from Belfast Mini Mill website

The final step is a rug yarn maker (figure 5), this machine creates core yarn, by wrapping the fibre around a core material (Belfast Mini Mill, 2009). This core material gives rugs the required weight to lay flat, as well as longevity and durability. Once the cored yarn is created it can be made into a rug through knitting, crocheting, weaving and braiding to create the final product of a rug (Belfast Mini Mill, 2009).
Figure 5: Rug Yarn Maker from Belfast Mini Mill website
If the mill expands, more machines, or attachments can be shipped over to expand the mill to create different types of fibre for various uses, or to reduce labour and time while using the mill (Belfast Mini Mill, 2009). Some pieces of machinery have been omitted, since the jobs can be done by hand, such as drying fibres, winding balls and skeins as well as smaller machinery has been suggested for ease of shipment (Belfast Mini Mill, 2009).
This product is created at the factory in Belfast, Prince Edward Island, Canada from raw materials directly from North America, with specifically 75% of materials coming from the United States, and 25% from Canada (Belfast Mini Mill, 2009). Belfast directly employs 22 employees, year round to assist in fibre creation, training, classes, production and maintenance and regularly sends parts and service employees world wide to service and maintain machines (Employment Journey, 2015).
FUNCTIONALITY
The size of labour force depends on the amount of fibre produced daily, Belfast suggests 2 people process 20 pounds of fibre a day (Belfast Mini Mills, 2009). The complete price of this four piece system is approximately $70,500 USD without shipping and taxes, this machinery can be used year-round and can be used by a community to make the price more realistic (R., 2016). With the washer costing $11,000 USD, the picker costing $8,000 USD, carder costing $45,000 USD and finally the rug yarn maker costing $6,500 USD (R., 2016). The inputs directly required are labour, soap, fibre conditioner, fibre, a core substance for the rug yarn maker, maintenance and space (Belfast Mini Mill, 2009). Indirectly the mill needs land to raise or grow the fibre producer on, feed and healthcare available to the animals when needed or fertilizer and pesticide for crops, as well as the labour and machines to clip the animals or harvest the crop. The market opportunity would be present in an agricultural community, where a group of farmers would purchase a share of the mill to use to create processed fibres or their own rugs. This product will not be purchased by one farmer, or a small group of farmers because of the high price. But the high price is worth it since both the finished product of a rug or the processed wool are both viable export options. Farmers can use fibres from animals that work on the farm, or create an additional investment of other animals and plants.
BENEFITS TO CANADA
The benefits to Canada can be seen on a mainly economic level from Belfast Mini Mill. Belfast provides a buisness model that is values local products and employees many people within north america (Belfast Mini Mill, 2009). Their machine shop is located in Belfast, Prince Edward Island in Canada and they use only materials from North America (75% from the United States, 25% From Canada). They employe 22 people year round and with this expansion they could increase their workforce and hire more Canadians to with the export and set up (Mackay, 2014). In their expansion to Asia, they can provide many of the options they give to local mill operators in Nepal, with the help of a translator, which would an additional set up cost (Belfast Mini Mills, 2009). They provide training in a very hands-on way, after set up the employees of Belfast can begin their training regime. Belfast’s training includes, instruction on set up, training in the operation of the mill in terms of processing, maintenance and safety. After a few months, a representative comes back and answers questions and reviews the processing technique being used (Belfast Mini Mill, 2009). Within every step of this training, hours can be logged for a translator and technician or a technician that speaks nepali.
If this mill becomes a popular item in the asian market, there is a potential to expand to accommodate this increase in business. This can be in the expansion of their warehouse, which would create more Canadian jobs for production of a bigger building, or a second building. As well if the market is expanded enough, there could be a need for a training building be set up somewhere accessible for the asian market. The coordinating, set up, and jobs created can be for Canadians, and you can have people processing fibre for a price per ounce or pound for a more profitable endeavour.
References:
Belfast Mini Mills. (2009). Retrieved October 11, 2016, from http://minimills.net/
MacKay, M. (2014, June 7). It's a small world after all at P.E.I.'s Belfast Mini Mill. The Guardian. Retrieved December 2, 2016, from http://www.theguardian.pe.ca/living/2014/6/6/it-s-a-small-world-after-all-at-p-e-i-s-3754375.html
R. (2016, October 17). Cost to set up a Mini Mill globally [E-mail to the author].
The Employment Journey. (2015, September 17). Hiring Practices - Belfast Mini Mills Ltd. Retrieved December 2, 2016, from http://employmentjourney.com/hiring-practices-belfast-mini-mills-ltd/